An Inside Look at PRS Body Sanding
Posted May 06, 2016
A vast amount of work goes into the production of a PRS guitar, but today we are going to focus in on just one step in the process, body sanding. If you’ve ever wondered how we do it and why there’s so much attention to detail, hopefully this blog will provide some answers!
—
For context, lets back up one manufacturing step before body sanding, the CNC body carve.
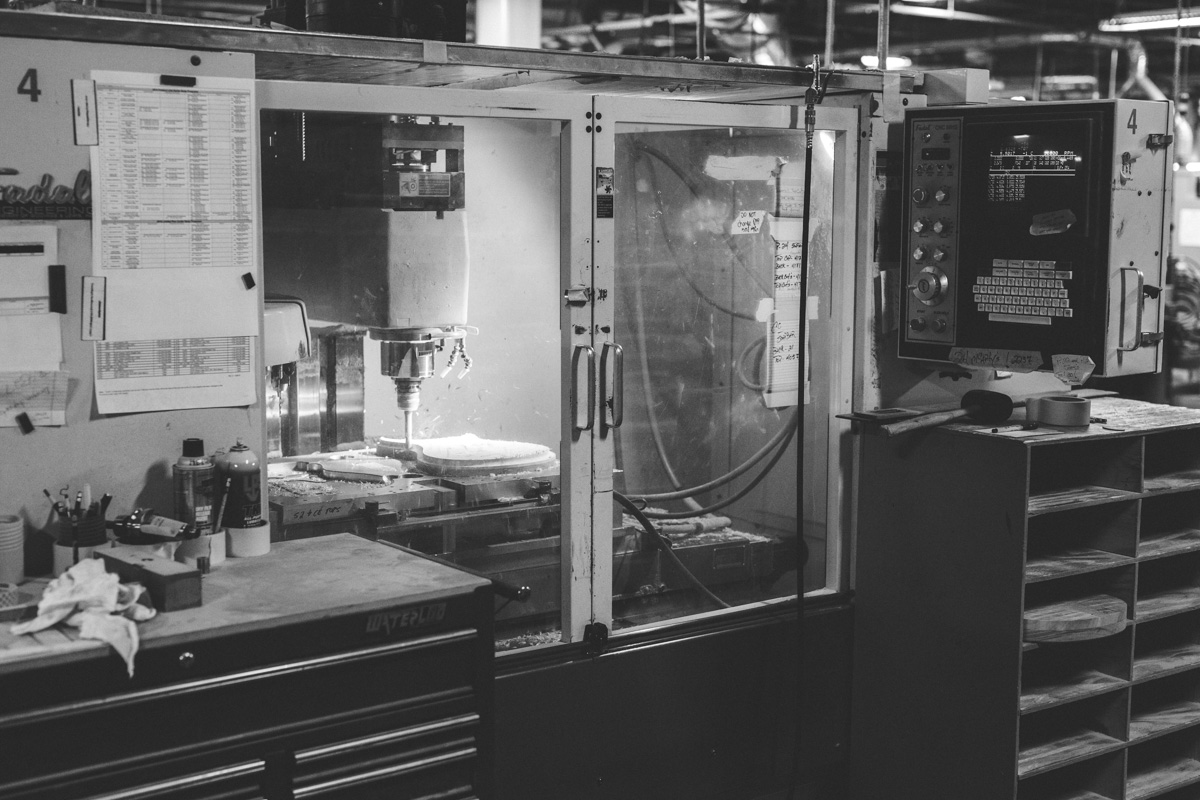
The guitar body comes out of the CNC machine cut to its rough shape, and covered in tool path marks and what we refer to as “tear out” — little marks on the body that need to be sanded out. This is where the body sanding team comes into play.
A supervisor will inspect the body for mineral or cracks in the wood, things that would typically require the body to be destroyed. If the body passes its inspection out of the CNC process, it is put into racks where the bodies will be distributed to our body sanding team. At any given time, we have about 30-40 guitar bodies in queue waiting to be sanded. This insures that we always have some instruments ready to be worked on.
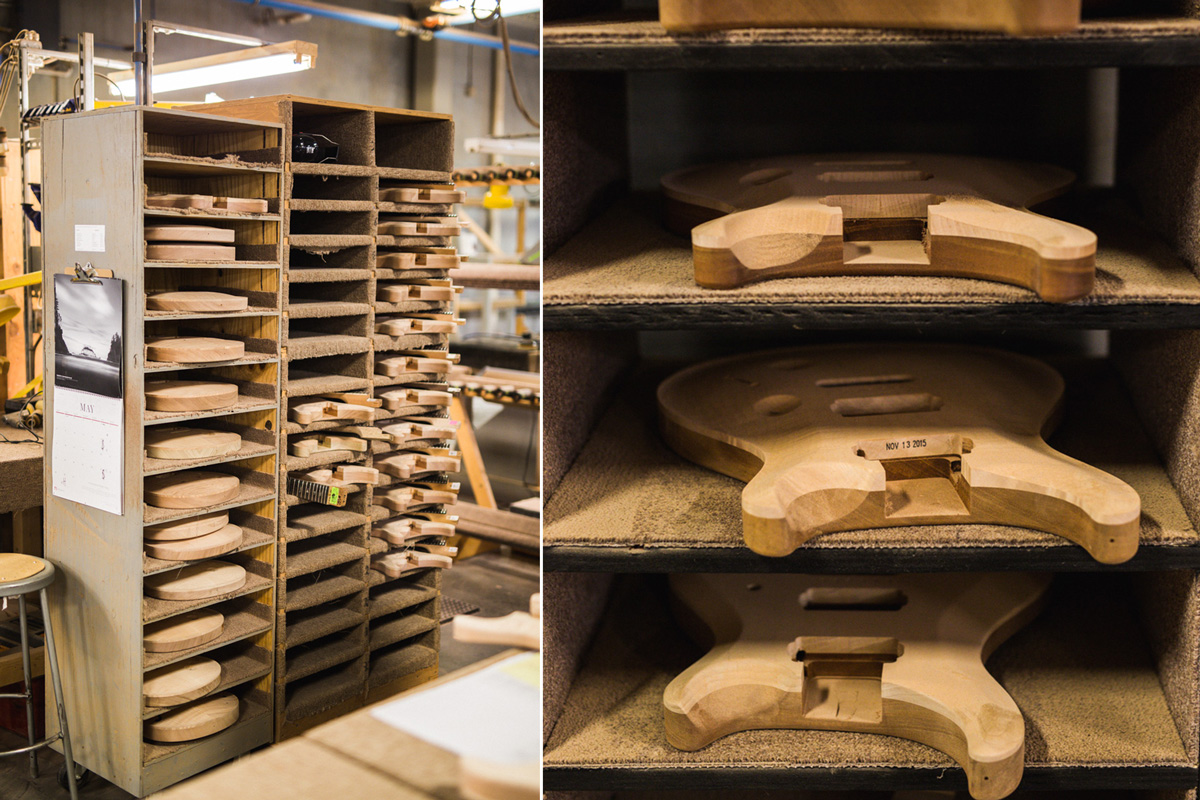
As you know, there are many different styles of PRS body shapes and models, and each one needs to be handled a bit differently. The more veteran sanders on the team will often handle models like the Hollowbody II, Santana, and other quilted-top models (which require a bit more finesse). The newer sanders on the team usually work on the flame-top guitars.
Typically, each employee on the team is responsible for 8 guitars a day and on average each guitar takes about 1 hour to sand. Newer employees in their first 3-9 months are often set with a goal of only 4 guitars a day so they are able to spend more time with each guitar and master the process. On average, it takes 9 months for a sander to get to the point where they can sand all types of models as well as 8 per day.
THE EQUIPMENT
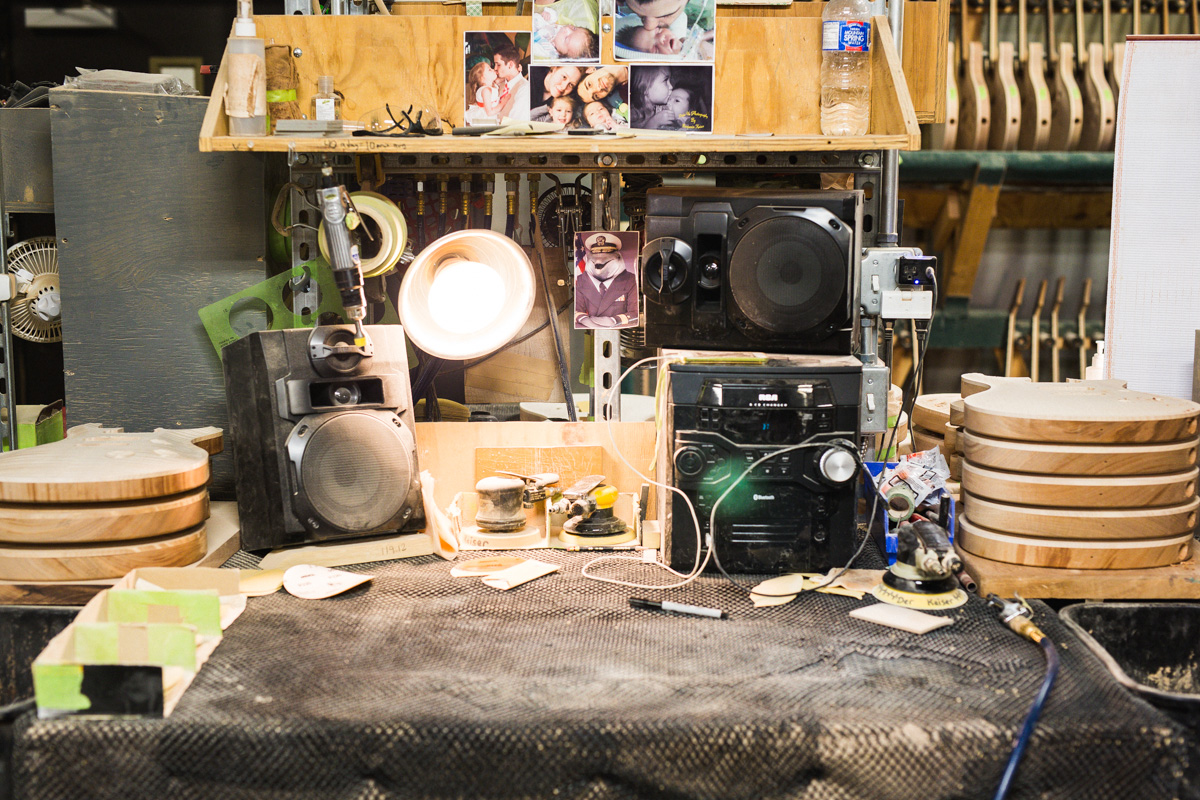
Employees have their very own work bench which they can set up however they’d like. All work benches are hollow in the middle and equipped with a down draft system. When engaged, the downdraft system sucks the sawdust away from the employees faces and through a filter. That’s why you’ll notice our employees don’t need to wear masks while sanding.
The body team uses varying grits of sandpaper to sand our guitars. Because each guitar needs to be handled and sanded differently, the grits used fall under the discretion of the employees. Typically though, they start with the lowest grit (80), and then move up to 150, 220, and 280. 80 grit is only used on the maple tops which tend to have more tooling marks and tear out from the CNC machines. The mahogany back and sides are started with 150 grit because of the softness of the wood.
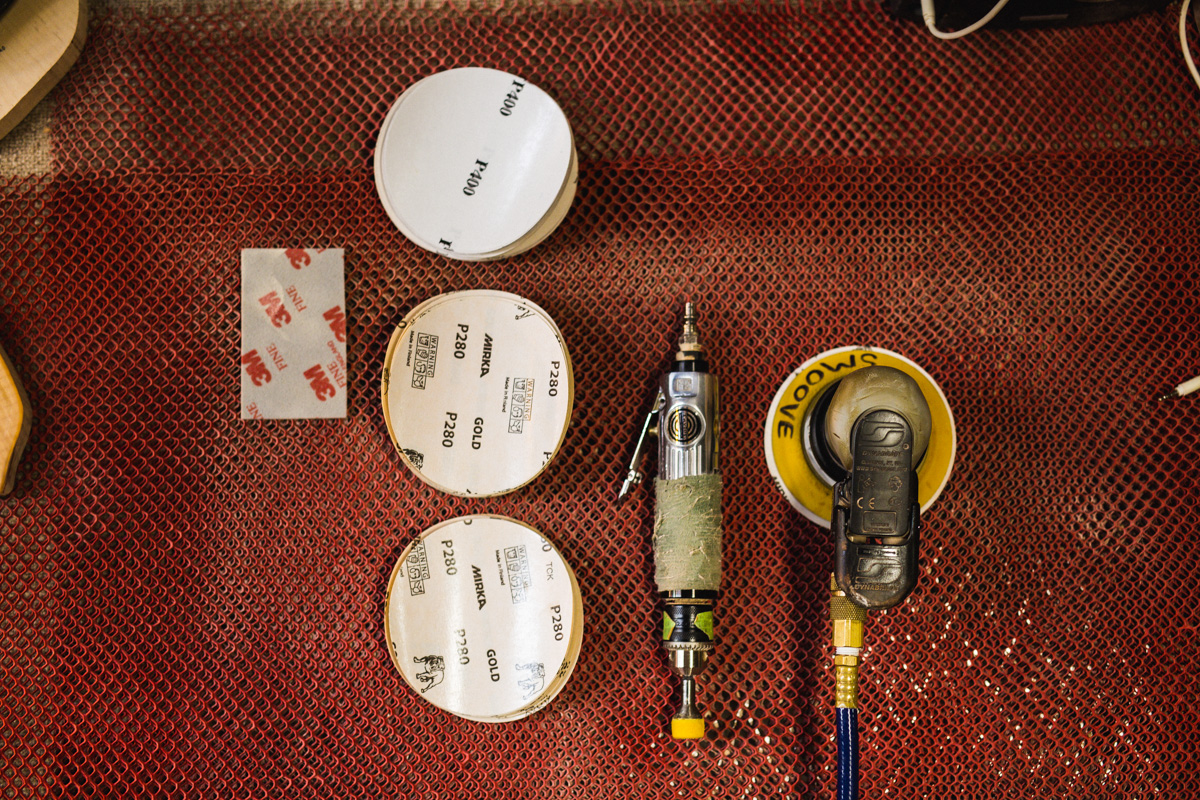
A number of tools are used to sand the guitars with fine detail. We use compressed air powered sanders that have dual action movement, meaning they spin as well as move in an elliptical pattern at the same time. We also use upright handheld drills for the smaller carves on the body like the knob contours.
The benches have an incredible amount of light which helps employees see the small details in the wood that need attention. Ultimately, the hands and eyes of our well-trained employees are the key to our quality.
THE TRAINING PROCESS
Before an employee is formally hired to the body team, they go through a trial-day where a supervisor can inspect their abilities and potential. The job requires an incredible amount of focus and attention to detail to get the body shape just right.
OUR QUALITY INSPECTION
All work is checked by a supervisor before it moves on to the next stage in manufacturing and this happens during every step in a PRS guitar’s life in the shop.
Employees will sign their initials inside the pickup cavity of the guitar to show who worked on it and to demonstrate our pride in quality!
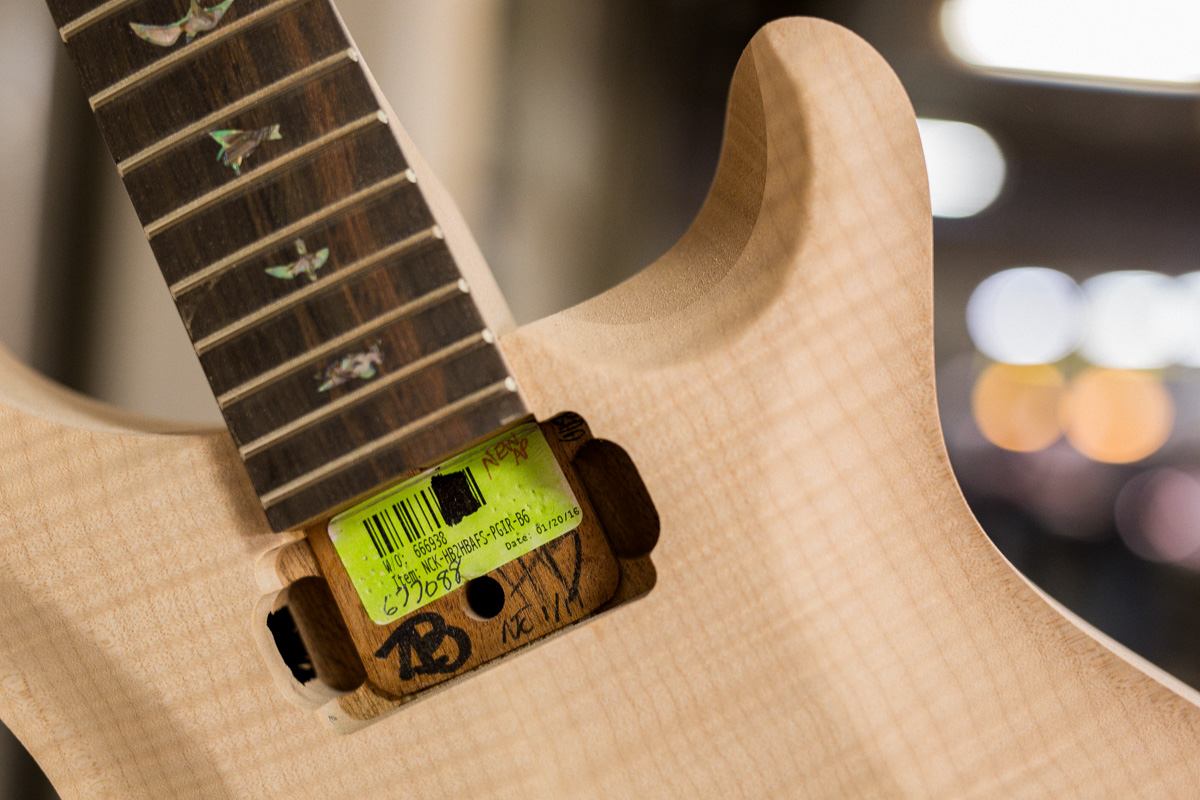
PRS doesn’t offer any “b-stock,” our policy is that a guitar won’t leave the shop unless it is to our exact, perfecting standards. The guitar is inspected closely by the supervisor who makes sure the guitar is true to the signature PRS body shape and carve, and that there are no dips/lumps or otherwise unsavory marks.
Sometimes in manufacturing things go wrong, an area of the body may be over sanded, or a crack in the wood might develop. As soon as this happens, the guitar is carefully inspected and if it doesn’t meet our standards of quality we destroy it. It’s sad to see this happen, but we want our guitars to be the best they can be and live a long life in our customer’s hands. Fortunately, our cut up rate is less than 5%!
Check out some photos below of our body sanders in action!
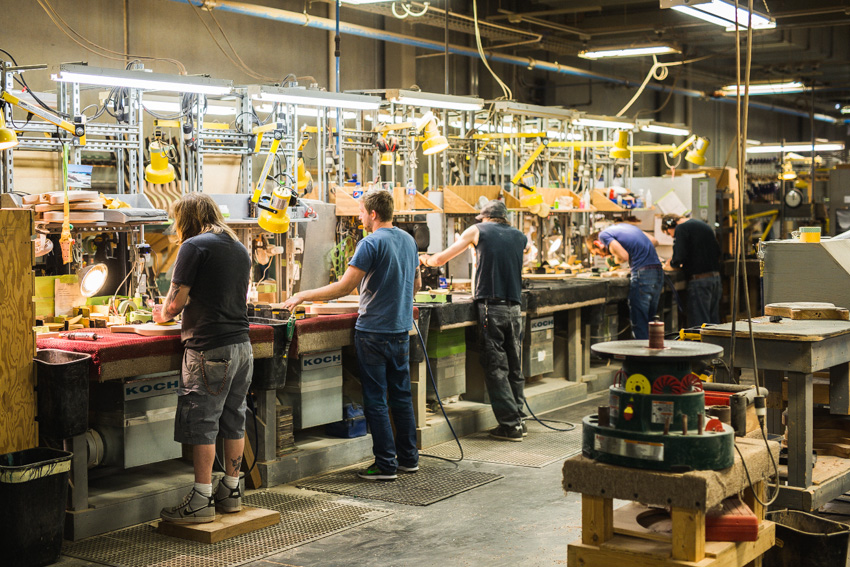
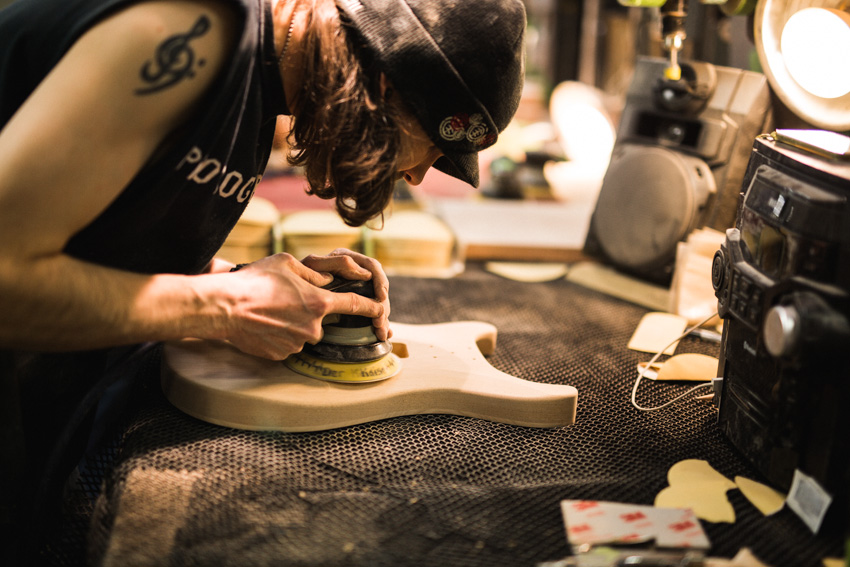
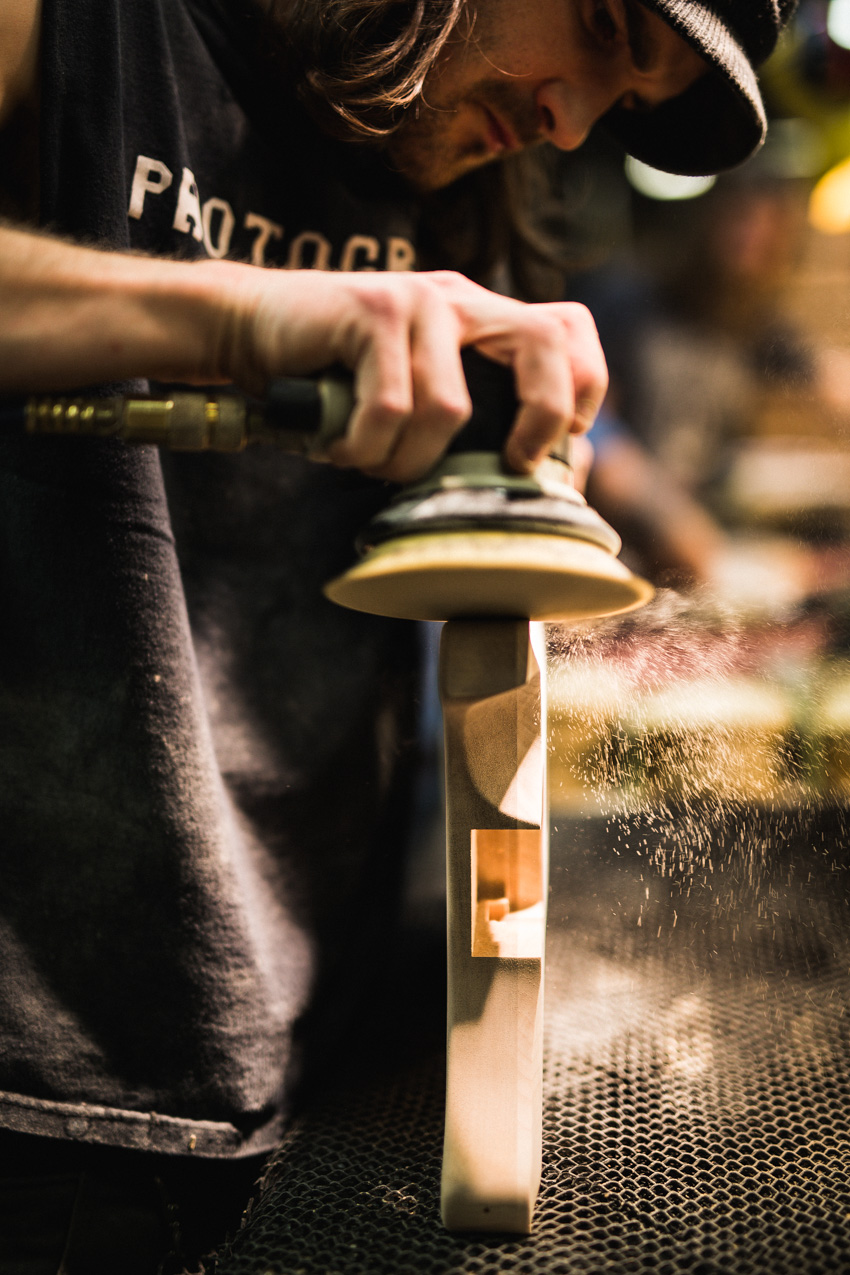
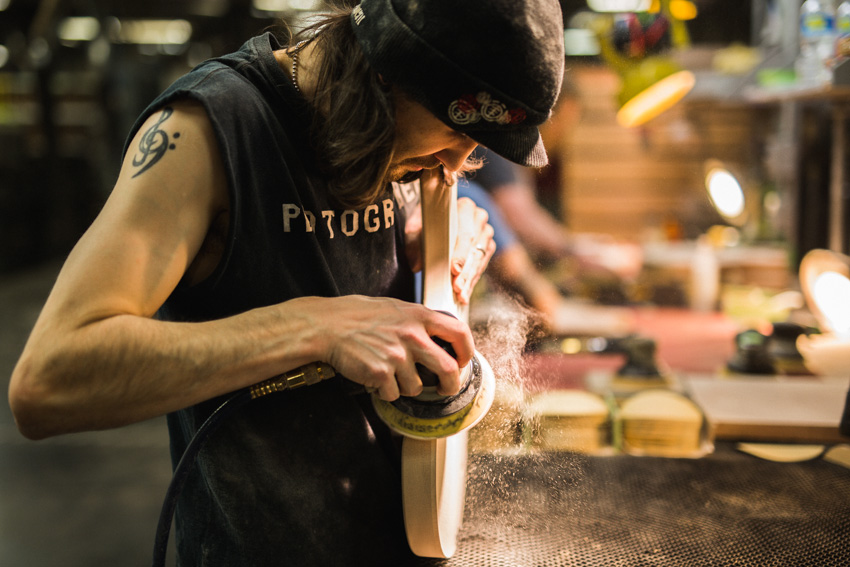
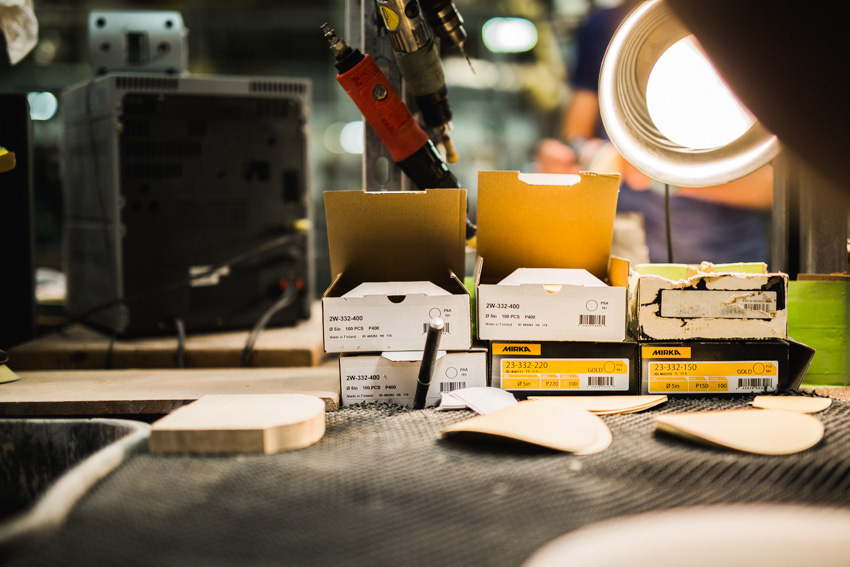
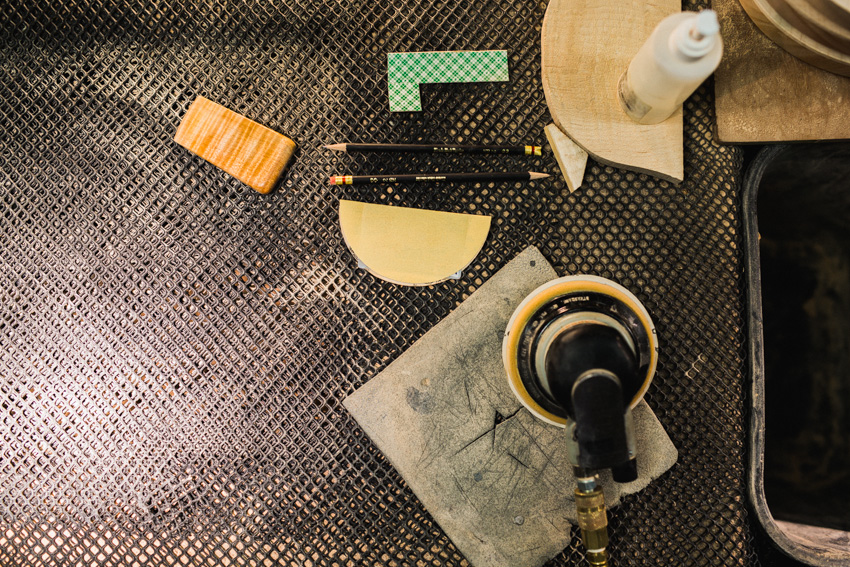
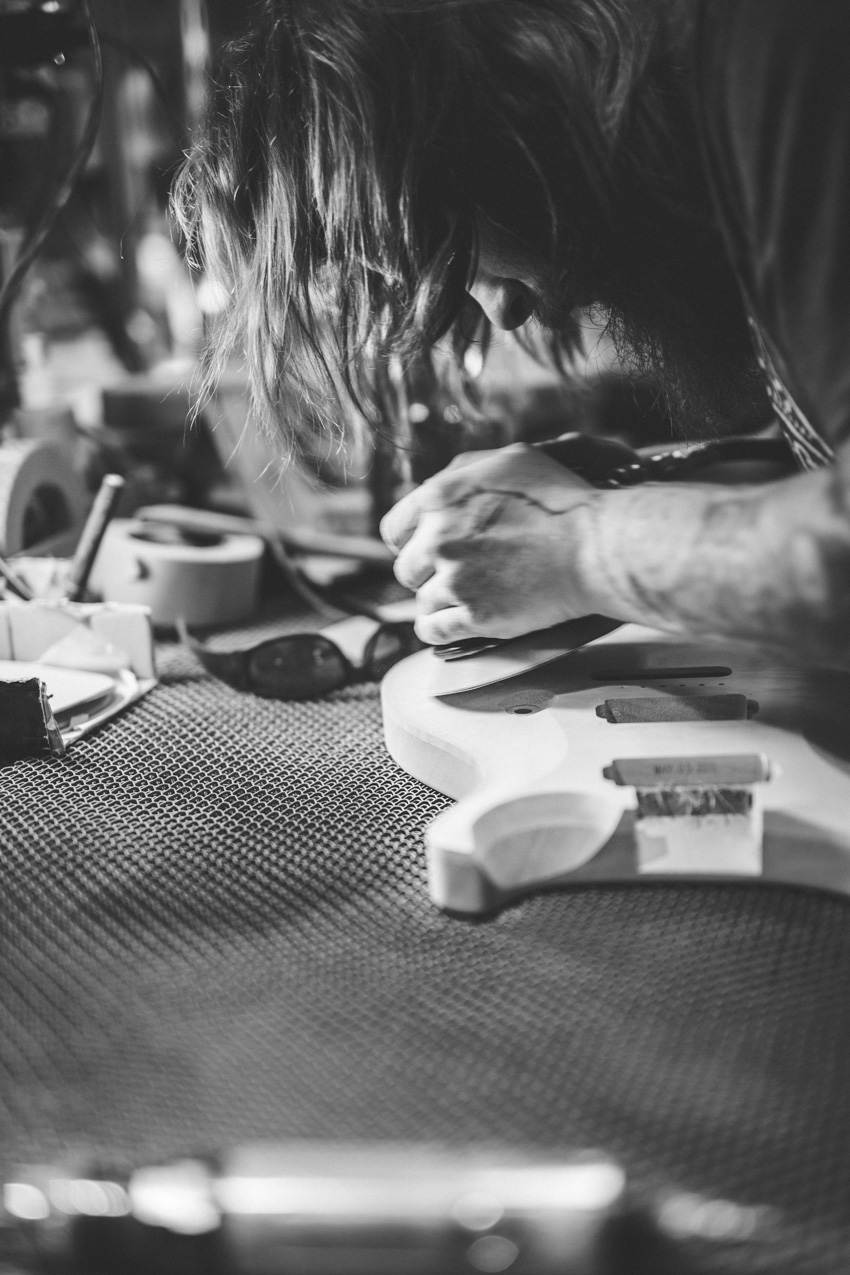
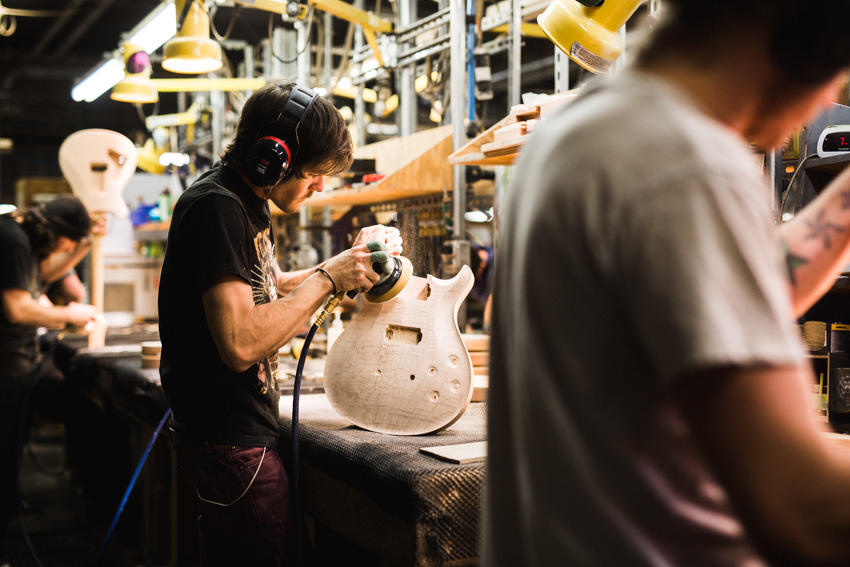
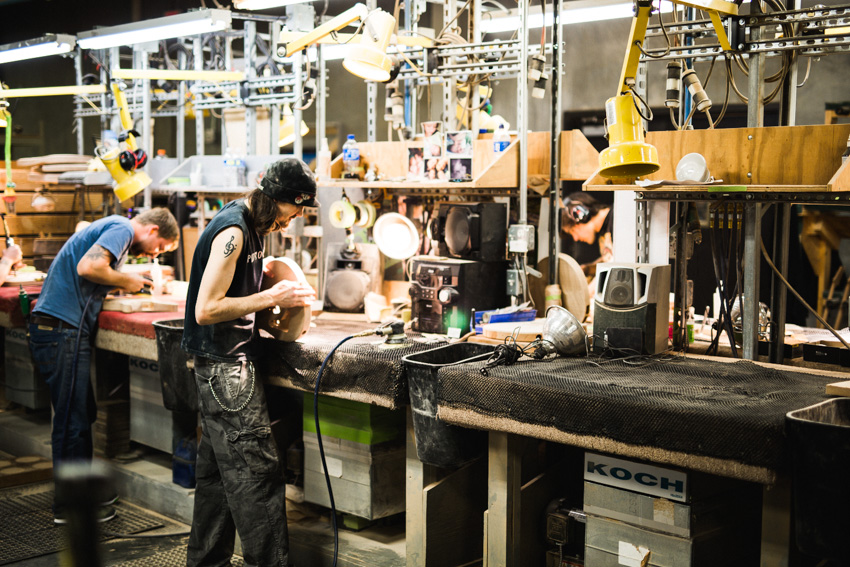
Think you have what it takes to be a member of the PRS body sanding team? Check out our careers page to see when we’re hiring!